强度考虑
来源:
|
作者:profed5ca94
|
发布时间: 2021-02-02
|
1730 次浏览
|
分享到:
塑件强度分为基本强度,持久强度、临界强度,临界强度很容易受到残余应力的影响。在这里重点介绍残余应力。
4.4塑件强度
塑件强度分为基本强度,持久强度、临界强度,临界强度很容易受到残余应力的影响。在这里重点介绍残余应力。
4.4.1塑料件残余应力产生过程
作为树脂内生应力的一个典型例子,残余应力是在不受外力作用的情况下由内部材料产生的一种应力。其大小取决于成型条件、成型品形状等多种因素。树脂注射成型时必然会产生残余应力,只是大小有别而已。其原因是在注射成型时,熔融树脂的表层和内层的固化收缩速度不同(存在时间差),于是固化慢的内部就会在固化的同时对固化快的外部产生拉伸作用,从而产生残余应力。
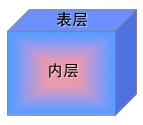
4.4.2残余应力所导致的问题
残余应力会导致部件变形、疲劳断裂、溶液膨胀加快等问题,因此必须预先了解并设法降低它。
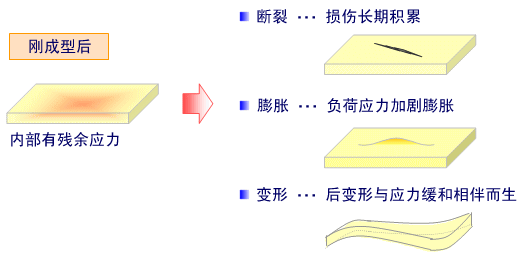
4.4.3残余应力测量方法
采用钻孔法(hole-drilling method)是评估金属材料残余应力的一种有效方法。其过程是贴上微型花式 3 向应变仪,在其中心部分钻孔(半断裂法),然后根据孔的变形情况来求出开放应力。ASTM(美国材料试验学会)已将此法标准化。
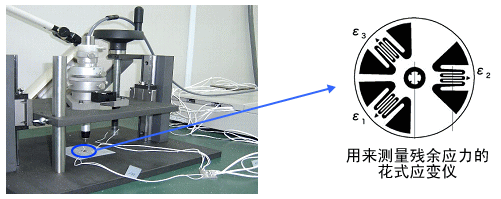
4.4.4钻孔法之原理
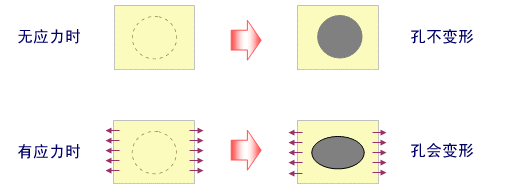
在毫无应力的试件上钻孔时孔将呈正圆形,而在有应力的试件上钻孔时孔则会产生应变。 这种应变的大小和方向与该处存在的应力有关,因此用设置在孔周围的 3 向应变仪来测量该应变后便可求出原有的残余应力值。
4.4.5传统方法的改进及其在树脂方面的应用
厚壁金属部件的应力均匀分布在测量范围内,而树脂成型品的薄壁处则分布有残余应力,因此用钻孔法来求出树脂成型品的残余应力时就要设法找到这种应力分布的适当表达方法。本公司经过认真研究测量方法和条件开发出了新的逐次计算法,从而能够定量评估残余应力在表层附近到内层的分布状况。
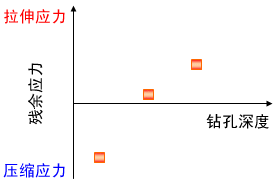
逐次计算法既可用来评估残余应力,也可用来评估树脂部件内层部分所承受的负荷应力。也就是说,可通过评估组装和加工(焊接、螺钉固定、弹性配合等)时树脂部件所承受的负荷来求出最佳制造条件的指标。
4.4 Strength Plastic
The intensity of the basic strength of plastic parts, lasting strength, the critical strength, the critical strength is vulnerable to residual stress. Here highlights the residual stress.
4.4.1 produce residual stress in the process of plastic
Health and stress as a resin a typical example, residual stress is the case without external force generated by the internal material of a stress. Its size depends on the molding conditions, various factors such as the molded shape. Resin injection molding would have a residual stress, but do not just size. The reason for the injection molding yes, the molten resin curing contraction of the inner surface and at different speeds (there is time difference), Yu Shi curing will slow the Neibu on curing in the curing of the Tong Shi Kuai's external production Lashenzuoyong, Conger produce residual stress .
4.4.2 the problems caused by residual stress
Residual stress will lead to part distortion, fatigue fracture, the solution to speed up expansion and other issues, it is necessary to understand in advance and try to reduce it.
4.4.3 Residual Stress Measurement
Using drilling method (hole-drilling method) is to assess the residual stress in metallic materials is an effective method. The process is affixed to the strain gauge micro fancy 3, in its central part of the drill (and a half break method), and then the deformation of the hole to find the opening stress. ASTM (American Society for Testing and Materials) has standardized this method.
4.4.4 Drilling Principles of Law
Stress in the specimen without drilling holes will show a circle, there is stress in the specimen will drill holes when the strain. The size and direction of this strain and the stress in the department there, so around the hole with a set of 3 to the strain gauge to measure the strain can be obtained after the original residual stress.
4.4.5 Improvement of traditional methods and the application of the resin
Thick-walled metal parts uniformly distributed in the measurement of stress within the resin molded thin-walled office while the residual stress distribution, hence the drilling method to calculate the residual stress molded resin should try to find that when the stress distribution appropriate expressions. The company, after careful study to develop measurement methods and conditions of successive new calculation method, which can quantitatively assess the residual stress in the vicinity of the inner surface of the distribution.
Successive calculation method can be used to assess the residual stress, can also be used to evaluate the resin parts of the inner part of the load stress. In other words, can assess the assembly and processing (welding, screws, elastic tie, etc.) when the load resin components to find the best indicators of manufacturing conditions.